Прецизионные отрезные станки
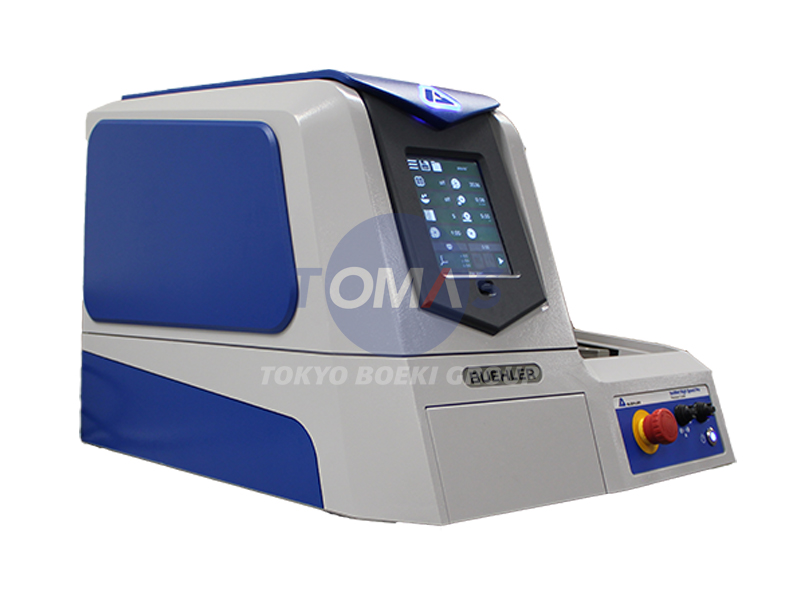
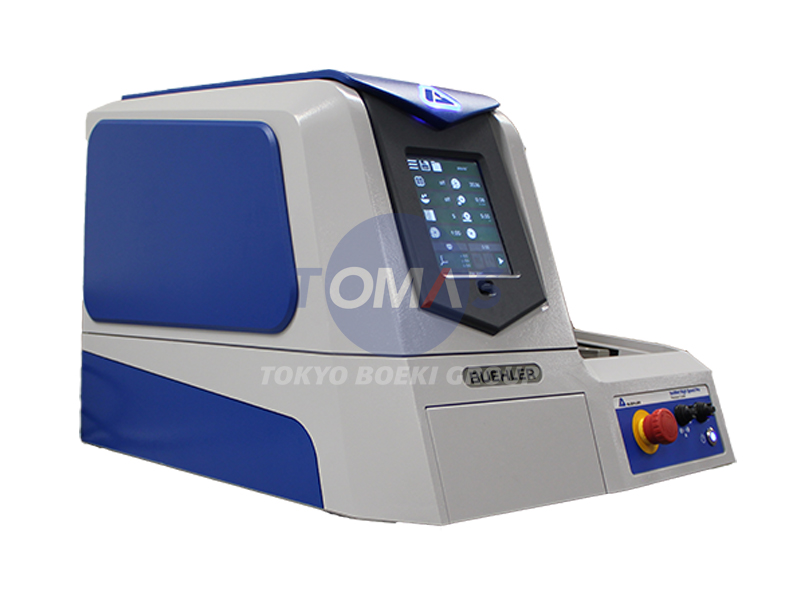
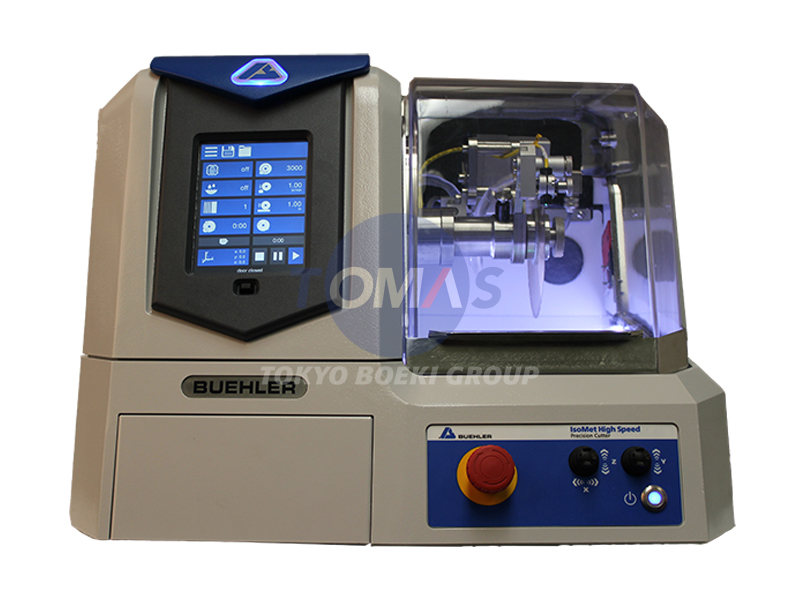
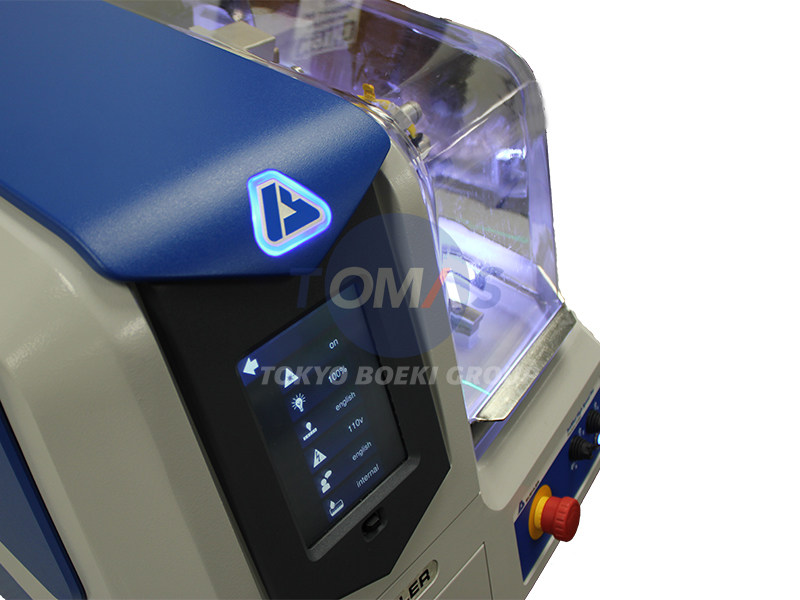
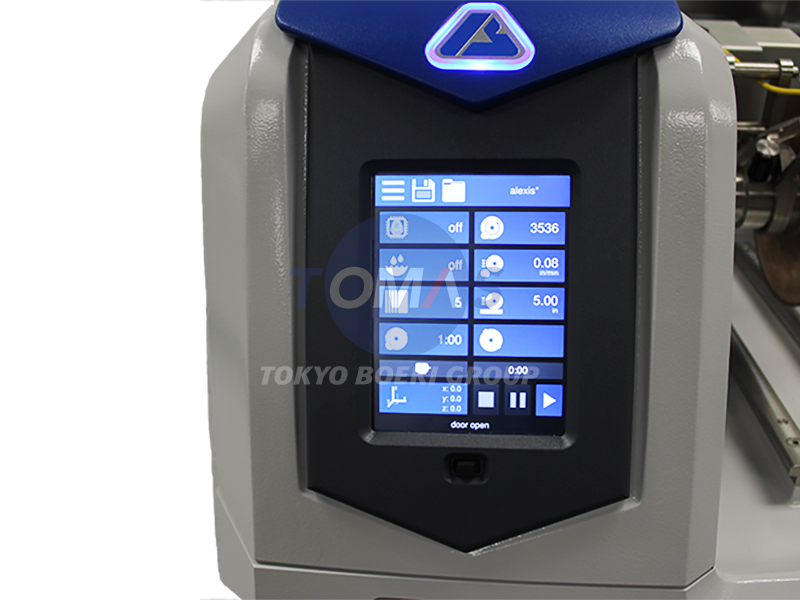
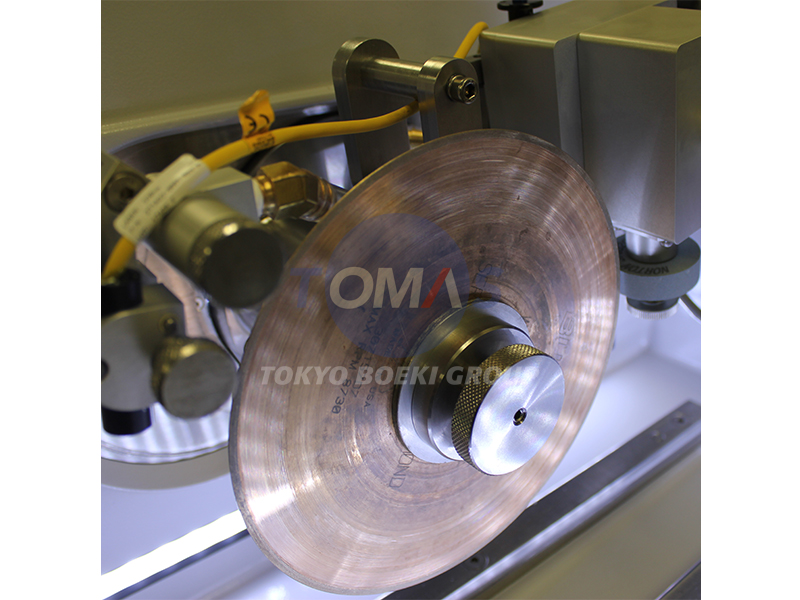
Автоматический прецизионный отрезной станок
(495) 223-40-00 | systems@tokyo-boeki.ru
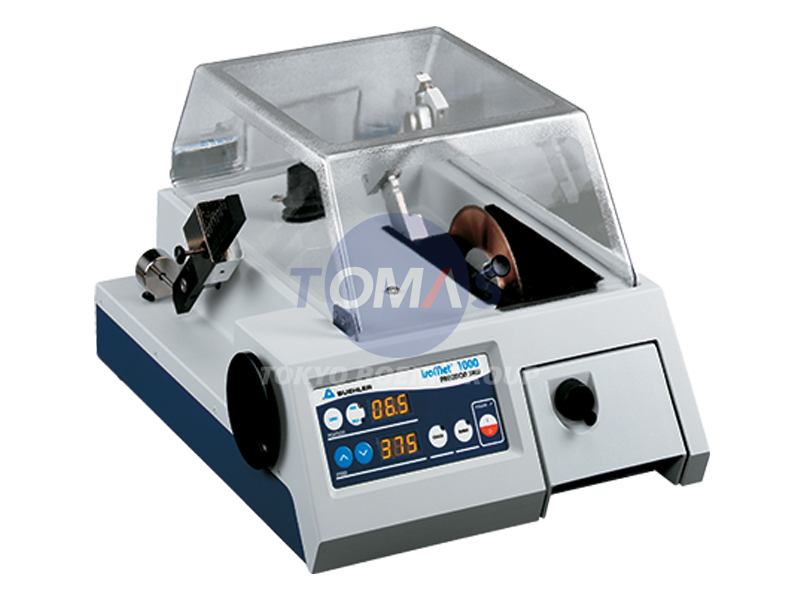
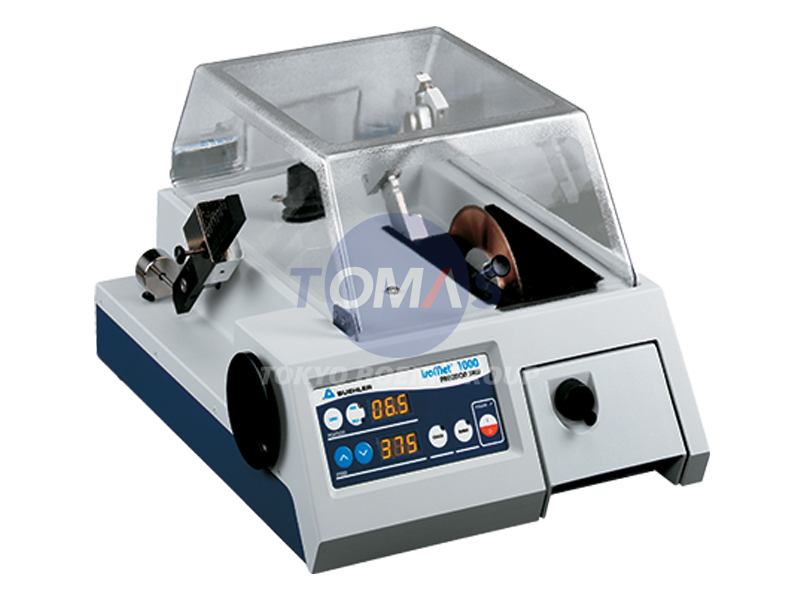
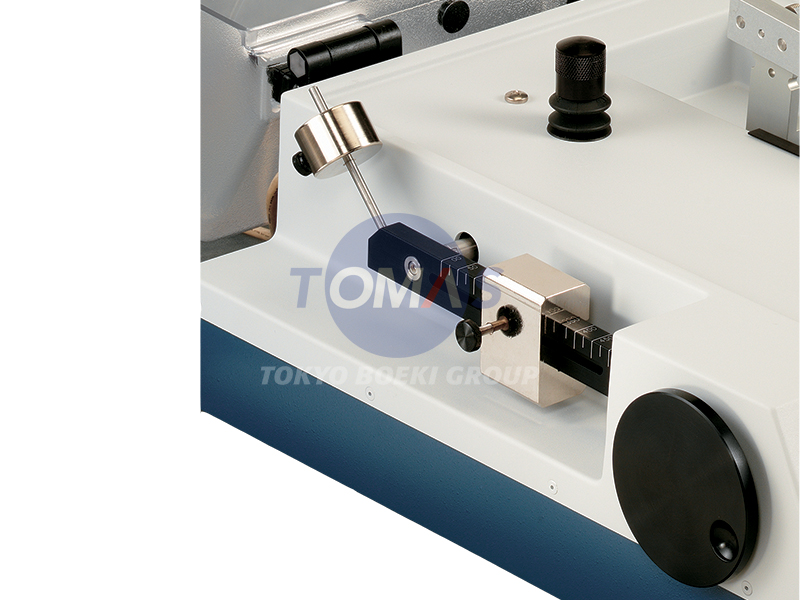
Прецизионный отрезной станок
(495) 223-40-00 | systems@tokyo-boeki.ru
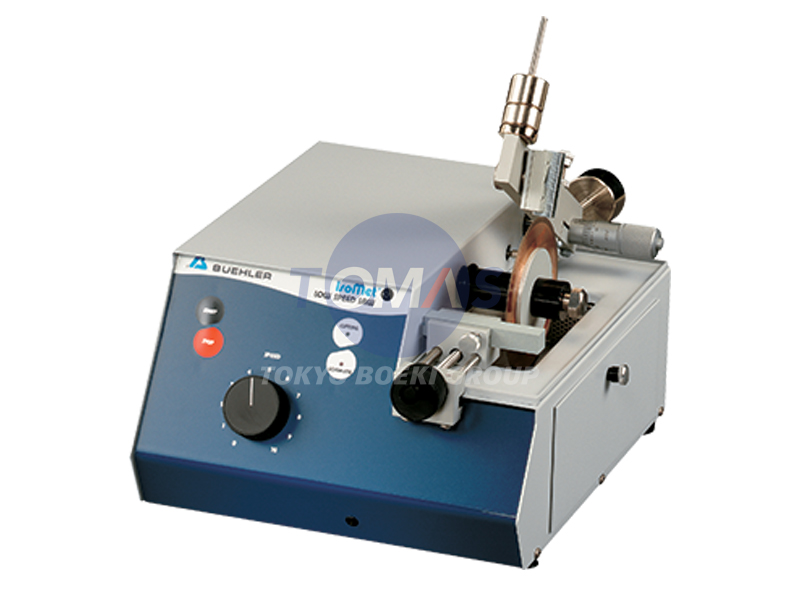
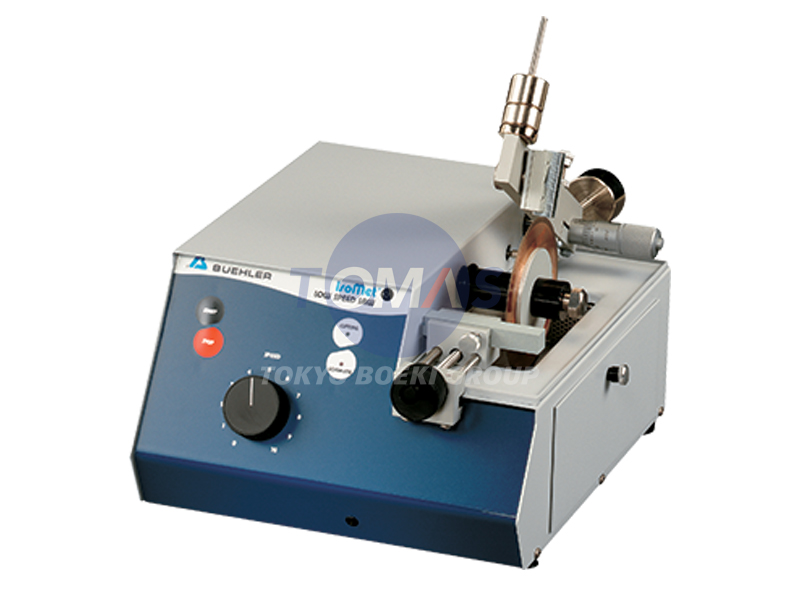
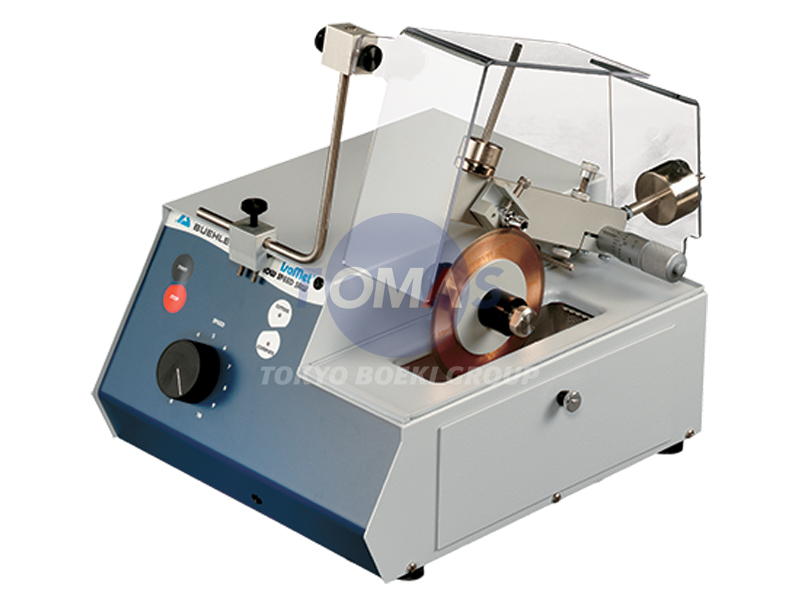
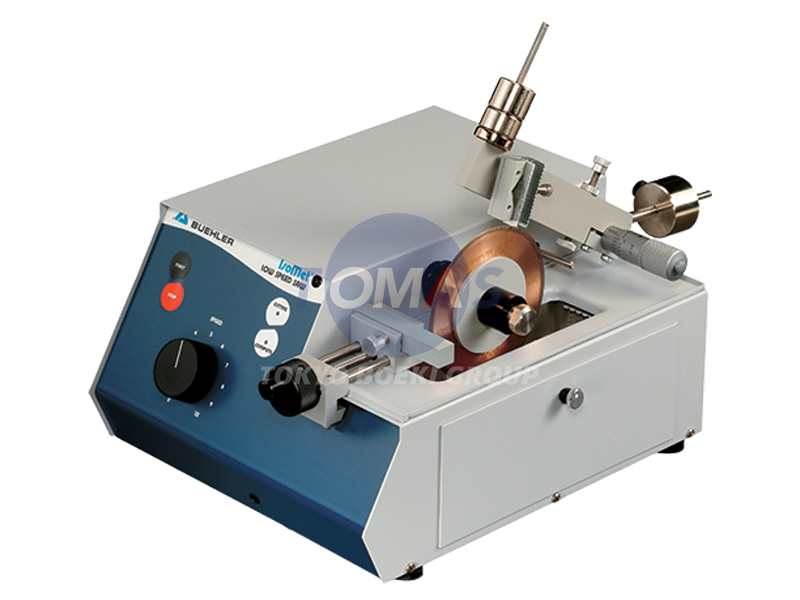
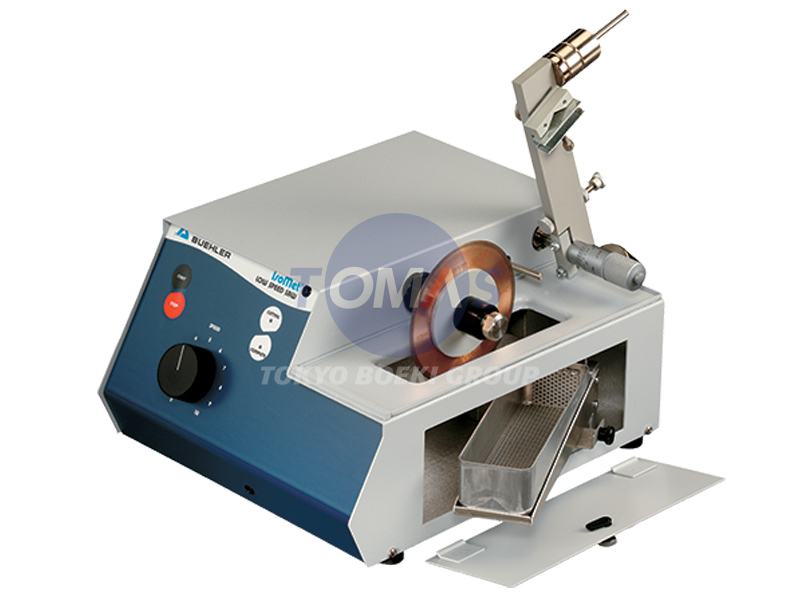
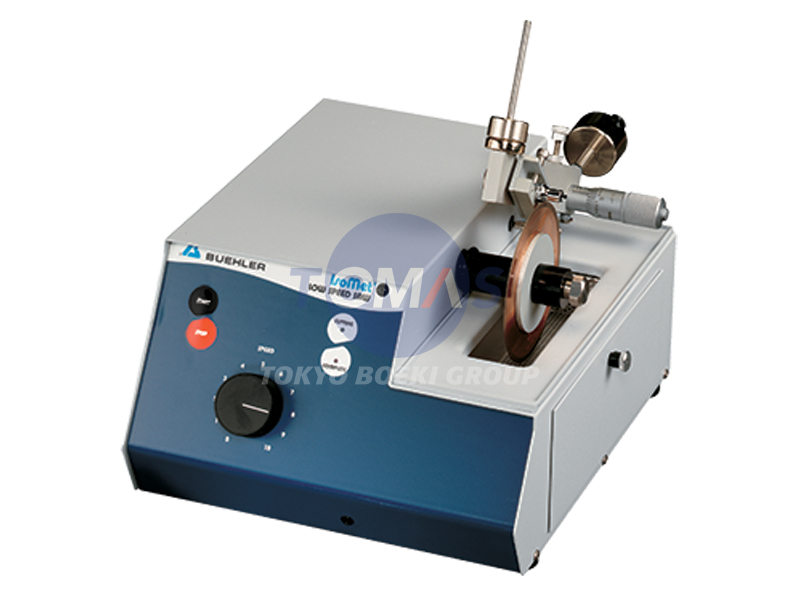
Прецизионный отрезной станок
(495) 223-40-00 | systems@tokyo-boeki.ru
Эффективная прецизионная резка
Современные модели прецизионных отрезных станков оптимизируют процесс резки и обеспечивают высокую эффективность, точность и единообразие результатов.
Прецизионная резка металлов и композитов – ключевой момент для проведения надежной, производительной диагностики и анализа образцов в широком сегменте отраслей промышленности. Например, для удовлетворения жестким требованиям к характеристикам материала в аэрокосмической промышленности применяются такие материалы, как металлы, комбинированные с усовершенствованными пластиками и композитами. Помимо необходимости иметь безупречную поверхность реза с точной геометрией образца, изменяются требования в целом к процессу контроля качества/обеспечения качества. Например, иногда требуется обрабатывать непрерывный поток образцов с большой производительностью и все возрастающей точностью. При больших объемах производства лаборатории приходится сталкиваться с задачами приготовления нескольких сотен образцов ежедневно.
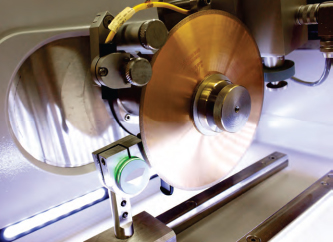
Цель прецизионной резки – минимизировать деформацию образца и получить безупречную поверхность для дальнейшего анализа
Для целей металлографических исследований, как правило, требуется разрезать деталь, что неизбежно ведет к разрушению структуры образца. Резка, первый этап металлографической пробоподготовки, создает деформированный слой на поверхности образца. Степень этой деформации зависит от технологии резки, типа оборудования, материала образца, типа отрезного диска (включая такие характеристики диска, как вид абразива, размер и концентрацию абразива, связывающий материал, толщина) и параметров резки, таких как скорость подачи, скорость вращения отрезного диска, скорость подачи охлаждающей жидкости и прочих регулируемых параметров.
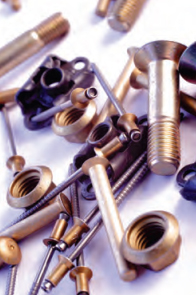
Надежность деталей крепежа имеет решающее значение для аэрокосмической промышленности. Они подвергаются жесткому контролю качества
Деформации образца в той или иной степени избежать при резке невозможно. По мере увеличения потока образцов и неизменно растущих требованиях к качеству резки, потребитель ищет решения для минимизации деформации. Резка на прецизионном станке позволяет производить рез с высокой точностью, чему способствует минимальная потеря материала на пропил, а также работать с хрупкими и рыхлыми образцами. Прецизионная резка обеспечивает также более высокое качество поверхности по сравнению с другими методами. Другое преимущество касается экономии времени: после прецизионной резки нет необходимости шлифовки на крупном абразиве, чтобы удалить слой поверхностной деформации, образующийся при других методах резки. Цель прецизионной резки – минимизировать деформацию и получить идеальную поверхность для анализа. Другие преимущества для лабораторий с большой загрузкой:
- Меньшие затраты времени и расходных материалов при последующей шлифовке и полировке.
- Большее количество образцов в день, что позволяет сотрудникам лаборатории сфокусироваться на других задачах.
Параметры резки
На процесс резки влияют три основных параметра: скорость вращения диска, характеристики диска, а также контроль нагрева и нагрузки на образец. Рассмотрим каждый из этих параметров.
Скорость вращения диска.
Ножовки, ленточные пилы, промышленные абразивные отрезные станки (обычно не имеют системы охлаждения) производят агрессивную резку со значительной деформации поверхности. Ножницы по металлу также существенно деформируют поверхность. Для выявления реальной структуры образца этот деформированный поверхностный слой должен быть удален.
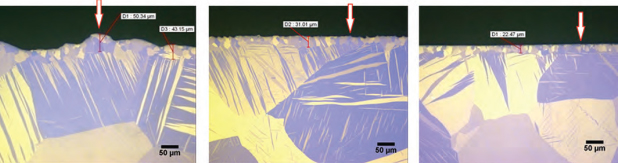
Деформация образца Zn после резки. а) Ленточная пила. Глубина слоя рекристаллизации 50 мкм. Неровная поверхность и большая глубина залегания двойников приведет к увеличению времени шлифовки; b) Абразивная резка. Глубина слоя рекристаллизации 30 мкм. Наблюдаются двойники. с) Прецизионная резка. Глубина слоя рекристаллизации 20 мкм. Минимальные следы двойникования.
Лабораторные станки, при правильном их использовании, наносят меньшее повреждение поверхности образца, чем промышленные станки. Для металлографических целей используются два основных типа станков. Первый тип – абразивные отрезные станки, где применяются абразивные диски. Диаметр диска обычно составляет 230 – 355 мм. Существуют станки и с б?льшими диаметрами отрезных дисков, до 450 мм, но обычно они находятся вне пределов лаборатории по причине их больших размеров.
Другой тип станков – низкоскоростные, которые в течение последних 30 лет претерпели трансформацию в прецизионные отрезные станки. Ранние модели низкоскоростных станков имели максимальную скорость вращения отрезного диска 300 об/мин и работали по принципу гравитационной подачи. Современные модели имеют максимальную скорость вращения отрезного диска 5000 об/мин и используют принцип линейной подачи наряду с другими опциями, такими как автоматическая система правки отрезного диска и автоматическая серийная резка. В данном типе станков могут применяться как расходуемые, так и не расходуемые отрезные диски.
Материал отрезного диска.
Алмазные отрезные диски на металлической основе могут иметь высокую или низкую концентрацию абразива с различными размерами абразивных частиц. Алмазные диски с высокой концентрацией абразива рекомендуются для резки металлов и полимеров (пластичных материалов) методом надрезания. При прохождении алмазных частиц через образец происходит процесс упрочнения прилежащего материала образца, он охрупчивается и разрушается.
Помимо концентрации абразива диски могут характеризоваться размерами абразивных частиц, с условной шкалой от 5 (мелкие) до 30 (крупные). Диск с размером абразива 10 будет иметь более купные частицы абразива, чем 5, однако это не означает, что они больше в 2 раза. Общее правило для подбора диска: чем меньше размер абразива, тем меньше деформация образца.
Контроль нагрева и нагрузки на диск.
Нагрев вызывается трением в процессе резки и приводит к деформации поверхности образца. Контроль нагрева – эффективный способ минимизировать деформацию. Применение очень тонких алмазных дисков в сочетании с надлежащим охлаждением помогает снизить степень нагрева, также как приложение строго необходимой нагрузки на диск в процессе резки. Правильный подбор диска и ограничение нагрузки позволяют практически полностью исключить поверхностную деформацию при подготовке образца для микроскопического анализа.
Опытный специалист лаборатории может определить, правильно ли прилагается нагрузка на отрезной диск, но при этом трудно обеспечить стабильность нагрузки на протяжении всего напряженного рабочего дня. Современное программное обеспечение контролирует ток двигателя и переводит эти данные в значение нагрузки на отрезной диск. С целью предотвращения перегрузки программное обеспечение дает сигнал станку снизить скорость резки по достижении заданного значения нагрузки. Поскольку программное обеспечение считывает значение тока двигателя, оператору больше нет необходимости принимать в расчет такие факторы, как состав материала образца и его толщина.
Другие усовершенствования конструкции отрезных станков касаются повышения точности и эффективности:
- Упрощение системы управления как сокращает процесс обучения персонала, так и способствует более надежному контролю за положением отрезного диска в процессе резки.
- Автономные системы фиксации образца позволяют подготавливать образец для установки, пока станок производит резку предыдущего образца. Таким образом, снижается время простоя станка.
- Инновационные системы правки отрезного диска очищают его от загрязнения, обнажая свежий абразив, что экономит время и повышает качество реза. В настоящее время конструкция многих станков предусматривает, что оператор будет производить правку диска до или после цикла резки. Это может привести к снижению скорости и качества даже в рамках одного цикла резки. Автоматическая система правки, такая как имеется у прецизионного отрезного станка IsoMet High Speed периодически вступает в действие в процессе резки и значительно увеличивает скорость, качество и воспроизводимость результатов.